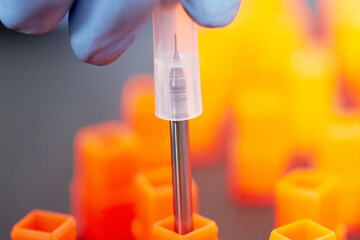
Best surface finishes and stable processes
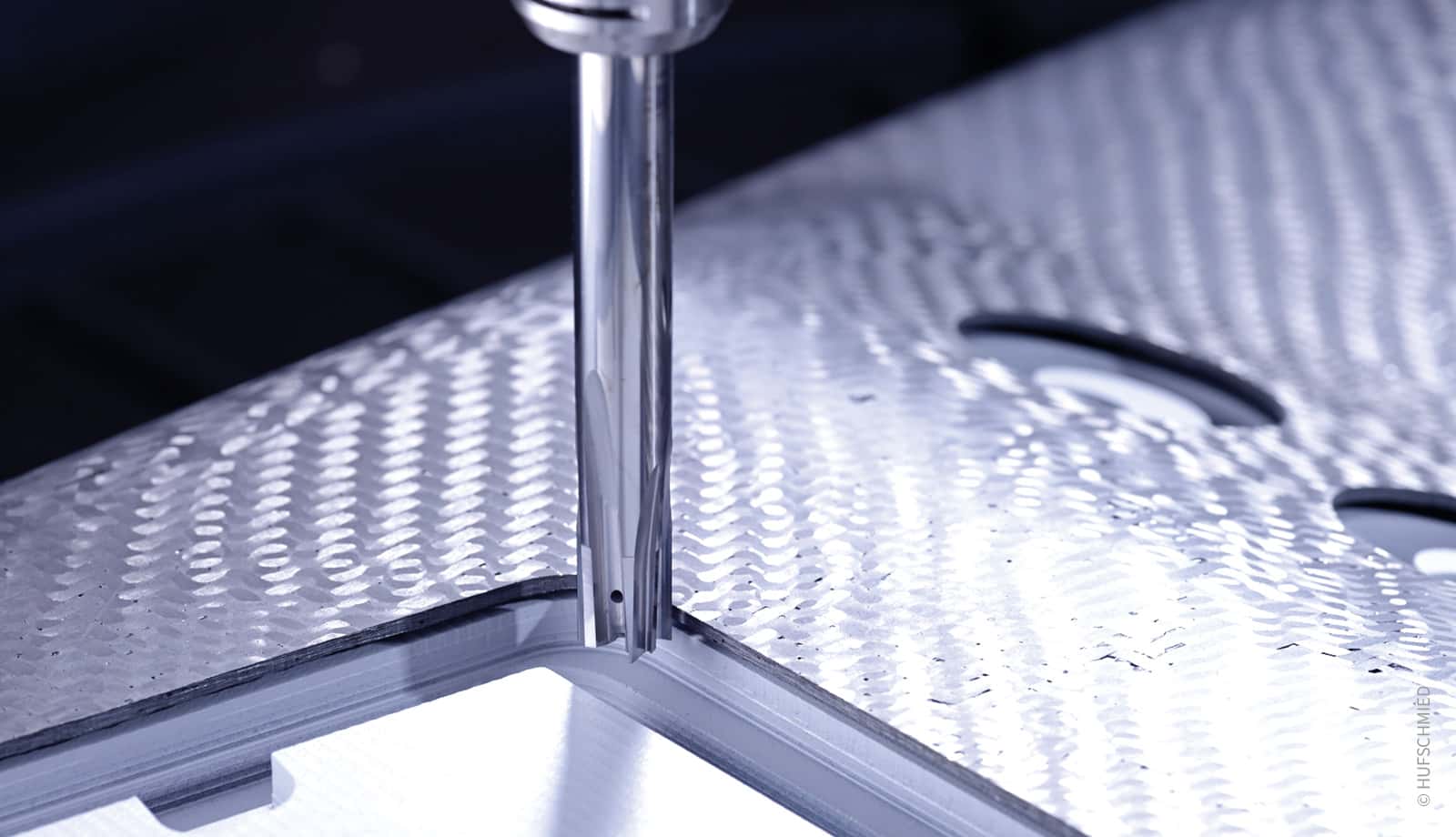
Engineering professionals jointly develop diamond-coated high-end tools
CFRP and GFRP, aluminum and titanium stacks, Peek, glass fiber-reinforced aluminum - if you want to machine modern materials reliably and at the same time faster and more precisely and with fewer machining steps, i.e. more productively, you need material-optimized tools and processes. HUFSCHMIED Zerspanungssysteme GmbH is exactly the right partner for this. Precision tools for new materials are the specialty of the family-owned company from Bobingen. Uncompromising quality standards are mandatory here for every detail. With the coordinated diamond coating DIP® – for example for CFRP machining – HUFSCHMIED therefore relies on the know-how of CemeCon, the global technology leader in diamond coating technology.
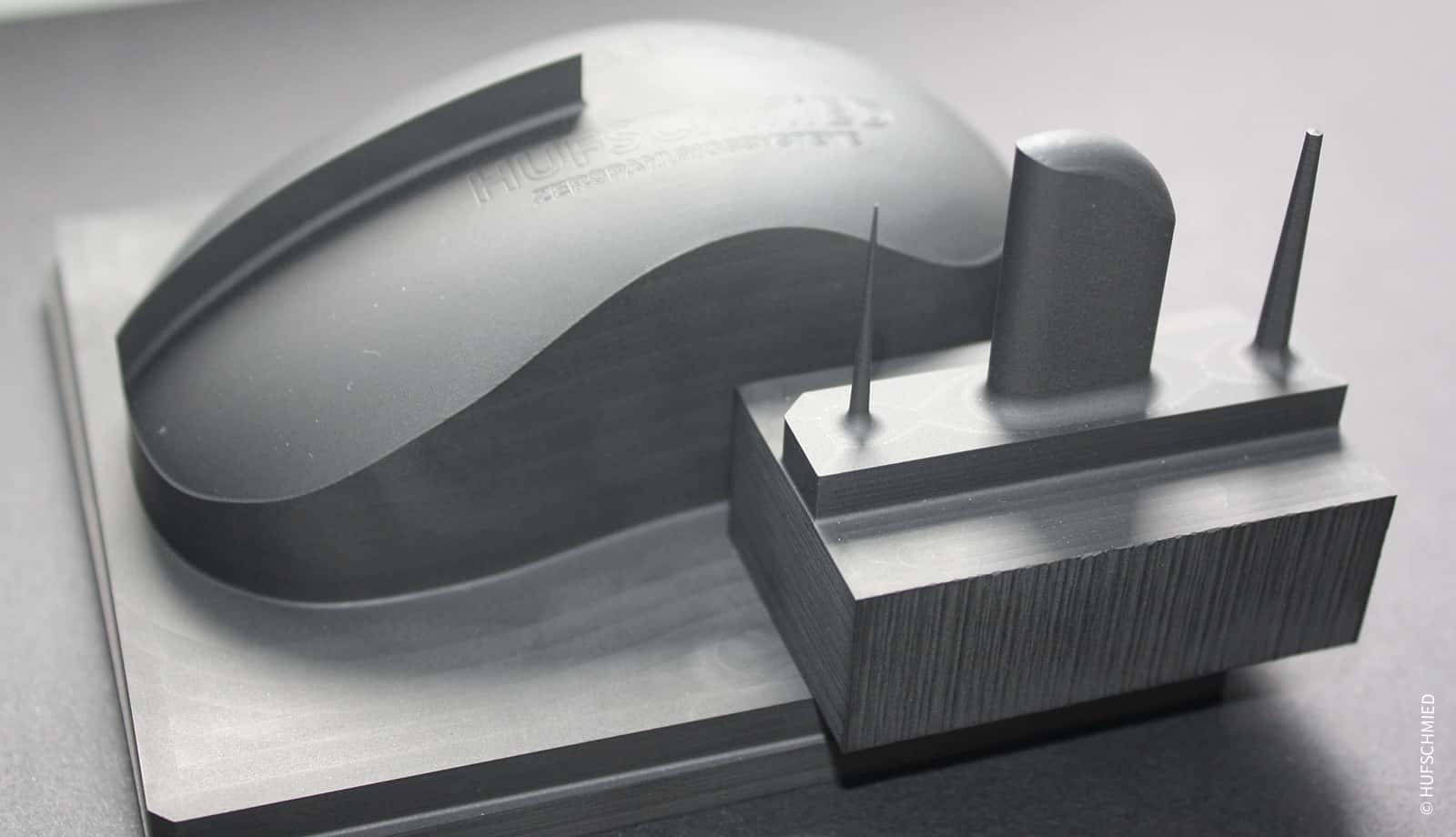
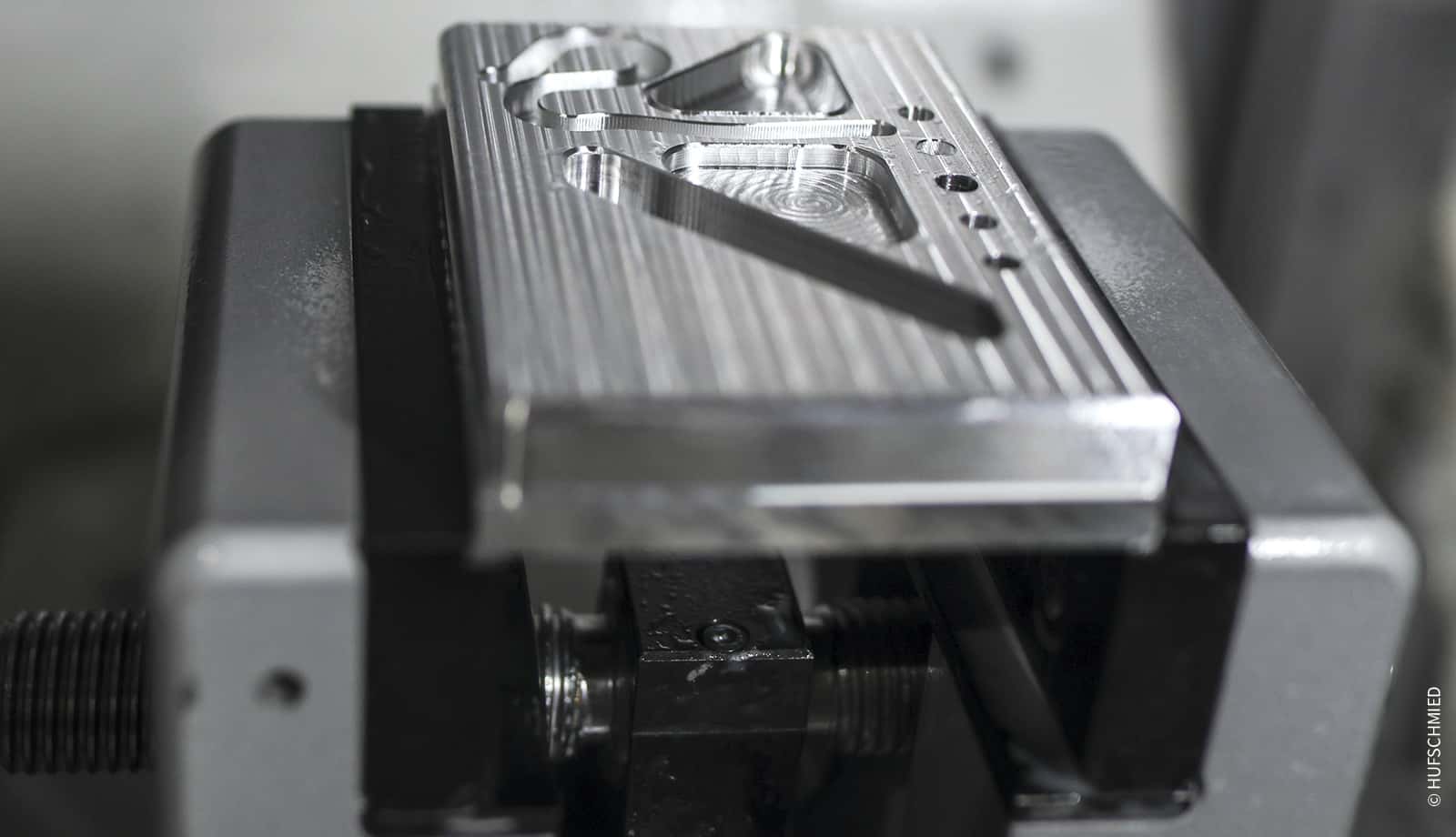
“Standard tools and processes have narrow limits – especially when it comes to machining high-tech materials. That's why we develop customized high-end solutions for machining. In order to be able to turn all the screws, we have created our own competence center: our Engineering Center in Bobingen. In addition to high-quality engineering tools and measuring equipment, our experienced specialists have the opportunity to reproduce, analyze and ultimately optimize the important parameters of the relevant processes on numerous machine tools. This makes the difference at the chip and ensures shorter cycle times, high process reliability, better machining results, and lower production costs,” says Dr Javier Fuentes, deputy head of development at HUFSCHMIED, describing the work of the tooling experts.
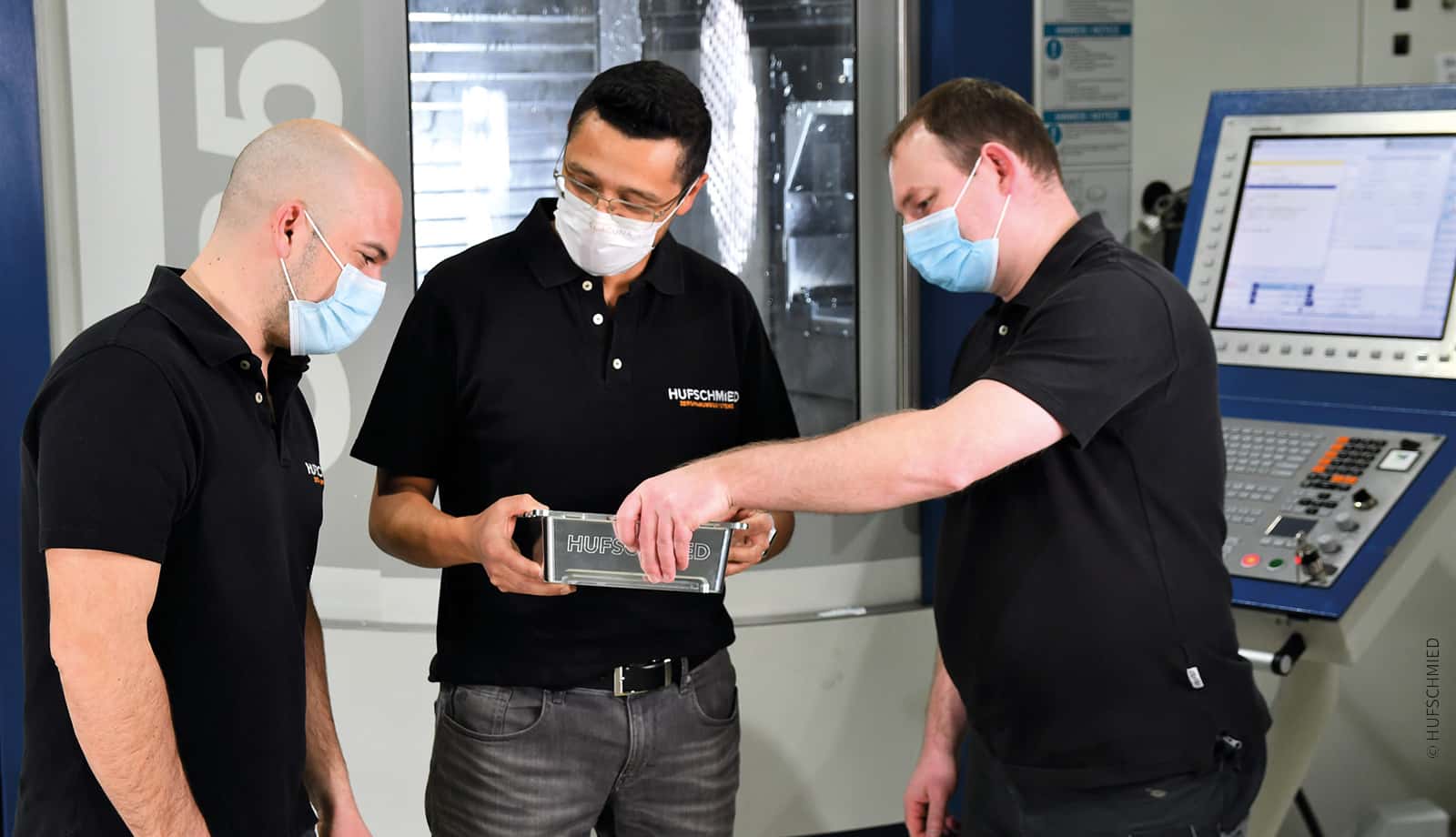
High quality is always a must in the development and production of the customized tools. In addition, especially for special projects, for example the automotive industry or medical technology, the traceability of the production chain is an important factor in manufacturing. Dr Javier Fuentes comments: “Here we are also increasingly using digital twins of our tools, where, for example, test certificates and the history of the tool are documented. This not only simplifies the management of the tools, but also opens up new possibilities in process monitoring: In this way, we can monitor and further improve the performance and service life of the tools as well as process reliability.”
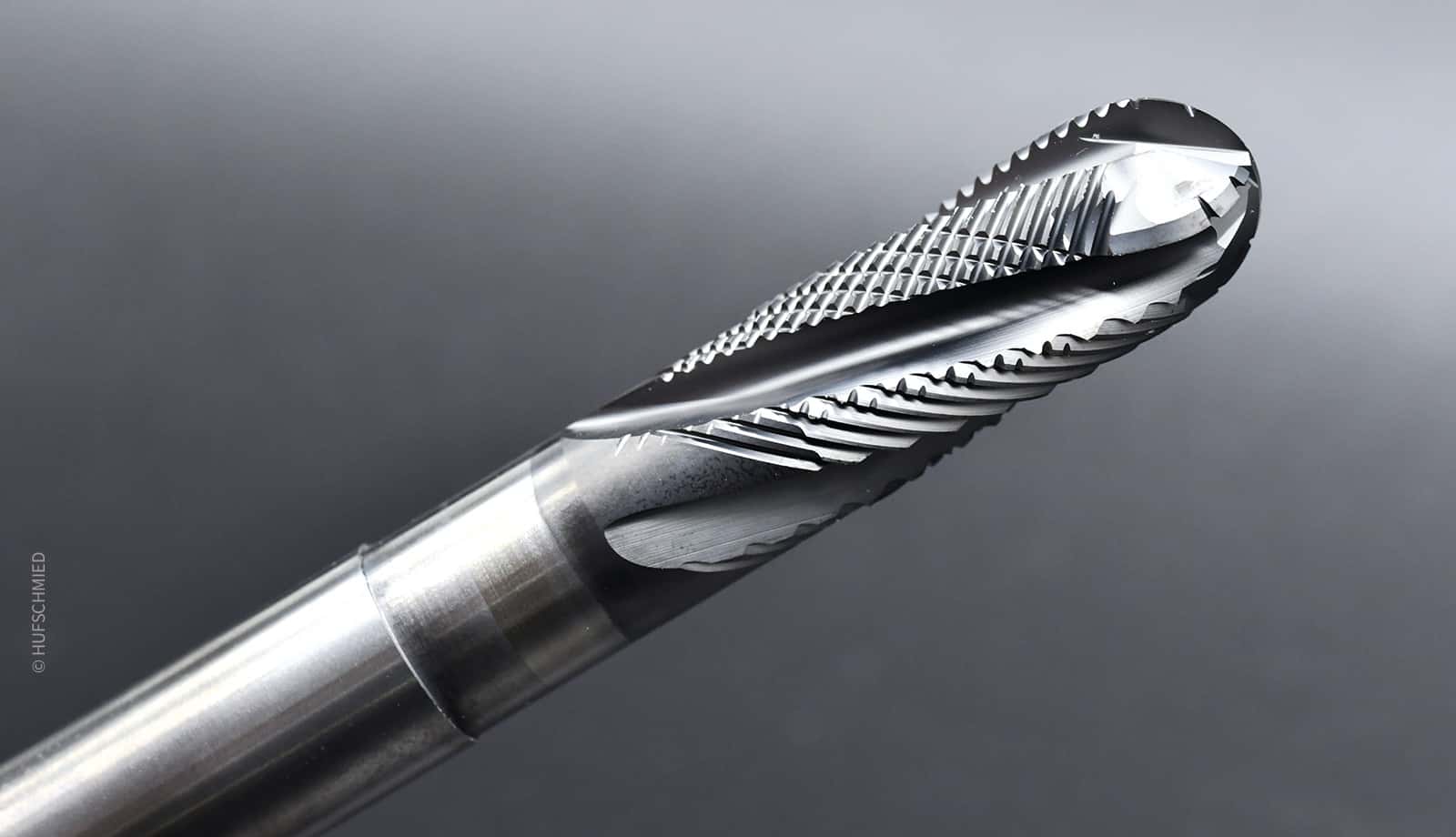
Matched diamond coatings for outstanding results
With e-mobility and the associated lightweight construction of vehicle components, the machining of CFRP and GFRP is becoming increasingly important in the automotive industry. Here, the question often arises as to which is better – PCD-tipped or diamond-coated tools. Diamond coatings have several advantages over PCD, knows Manfred Weigand, Product Manager Round Tools at CemeCon: “With diamond coatings, more complex geometries and thus significantly more diverse machining solutions can be implemented than with PCD. In addition to twisted cutting edges, which are only feasible to a limited extent with PCD, diamond coatings also enable, for example, complex chipbreakers, compression or roughing cutting edges as well as multiple cutting edges. Diamond-coated tools also allow higher feed rates and speeds. Another plus is that the cost of PCD is usually many times more expensive than diamond coatings.”
At CemeCon, as with us, the ENGINEERING PROCESS is also a central component in the DEVELOPMENT OF CUSTOMIZED SOLUTIONS for special applications. Our DIAMOND COATING DIP® is the result of our successful cooperation: it allows us to INDIVIDUALLY MATCH the tool and the coating, thus ensuring the BEST SURFACE QUALITIES.
Dr Javier Fuentes, deputy development manager at HUFSCHMIED.
The combination of geometry, substrate and coating plays a special role and requires individual coordination. “At CemeCon, as with us, the engineering process is also a central component in the development of customized solutions for special applications. Our diamond coating DIP® is the result of our successful cooperation: it allows us to individually match the tool and the coating, thus ensuring the best surface qualities,” Dr Javier Fuentes is pleased to report. The nanocrystalline and smooth surface structure prevents dust adhesion and ensures high tool life. At the same time, the milling cutters are also optimally protected against chemical influences and against aggressive mechanisms that can arise with abrasive and inhomogeneous materials such as CFRP.
Successful in use
Also for Elbe Flugzeugwerke GmbH (EFW), expert for the development and production of lightweight components for aviation and partner of Airbus, HUFSCHMIED has already developed coordinated tools for the machining of fiber-reinforced plastics (FRP), which have already proven themselves in practice many times: “With tools by HUFSCHMIED, we were able to significantly improve the machining process when machining reinforced CFRP floor beams for the Airbus A350. In terms of unconditional avoidance of delamination, well predictable tool behavior and smoother machining, HUFSCHMIED tools are the first choice for us in this particular process.” Reason enough for EFW to recommend the tool manufacturer as a development partner and tool supplier for all applications in which limits of what was previously possible are reached.
HUFSCHMIED
Founded in 1991 HUFSCHMIED Zerspanungssysteme GmbH develops and manufactures process-optimizing precision tools. In doing so, the family-owned company from Bobingen specialized early on in the machining of plastics, glass fiber materials and carbon fiber and is today one of Europe's leading manufacturers of cutting tools for new materials. The matched tools are produced in-house in Germany using state-of-the-art manufacturing methods. High-precision 3D measuring machines of the latest generation ensure the high quality. In continuous dialog with universities, machine builders and users, HUFSCHMIED continues to drive the development of process-optimizing tools of the highest quality. Tools and process consulting from HUFSCHMIED are especially appreciated in the automotive and aerospace industries as well as in medical technology.