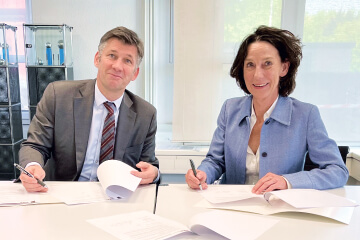
Hard, harder, SteelCon®
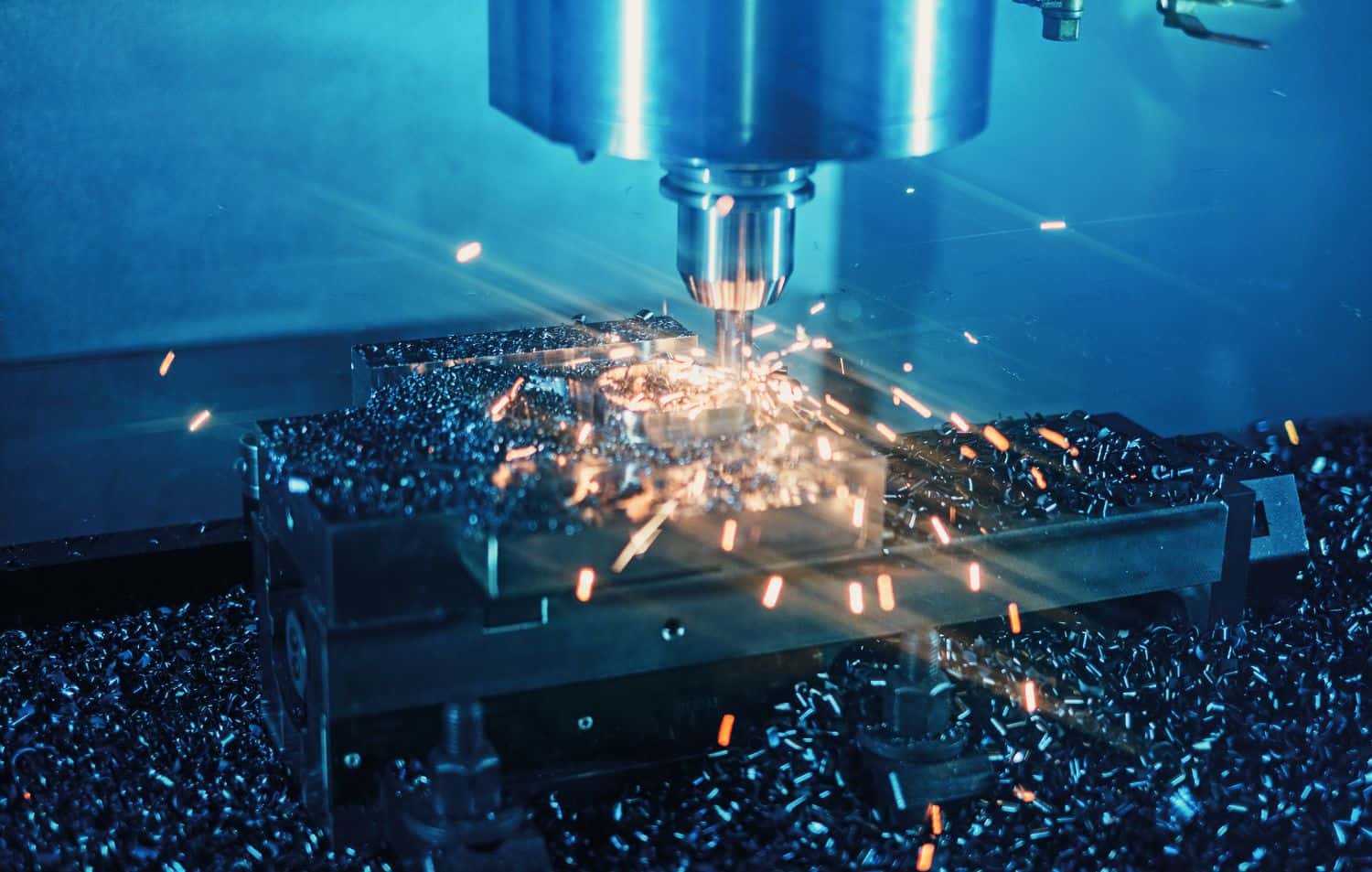
More performance in the machining of hardened steel for injection molds
In tool and mold making, the machining of hardened steels beyond 50 HRC is standard. It nevertheless remains a discipline for specialists, especially for manufacturers of precision tools. The milling cutters used are subject to very heavy wear. Tool manufacturers therefore know that long and, above all, process-reliable tool life is only possible with a coating adapted to the tool. With the new HiPIMS coating material SteelCon®, CemeCon now offers the best solution for this.
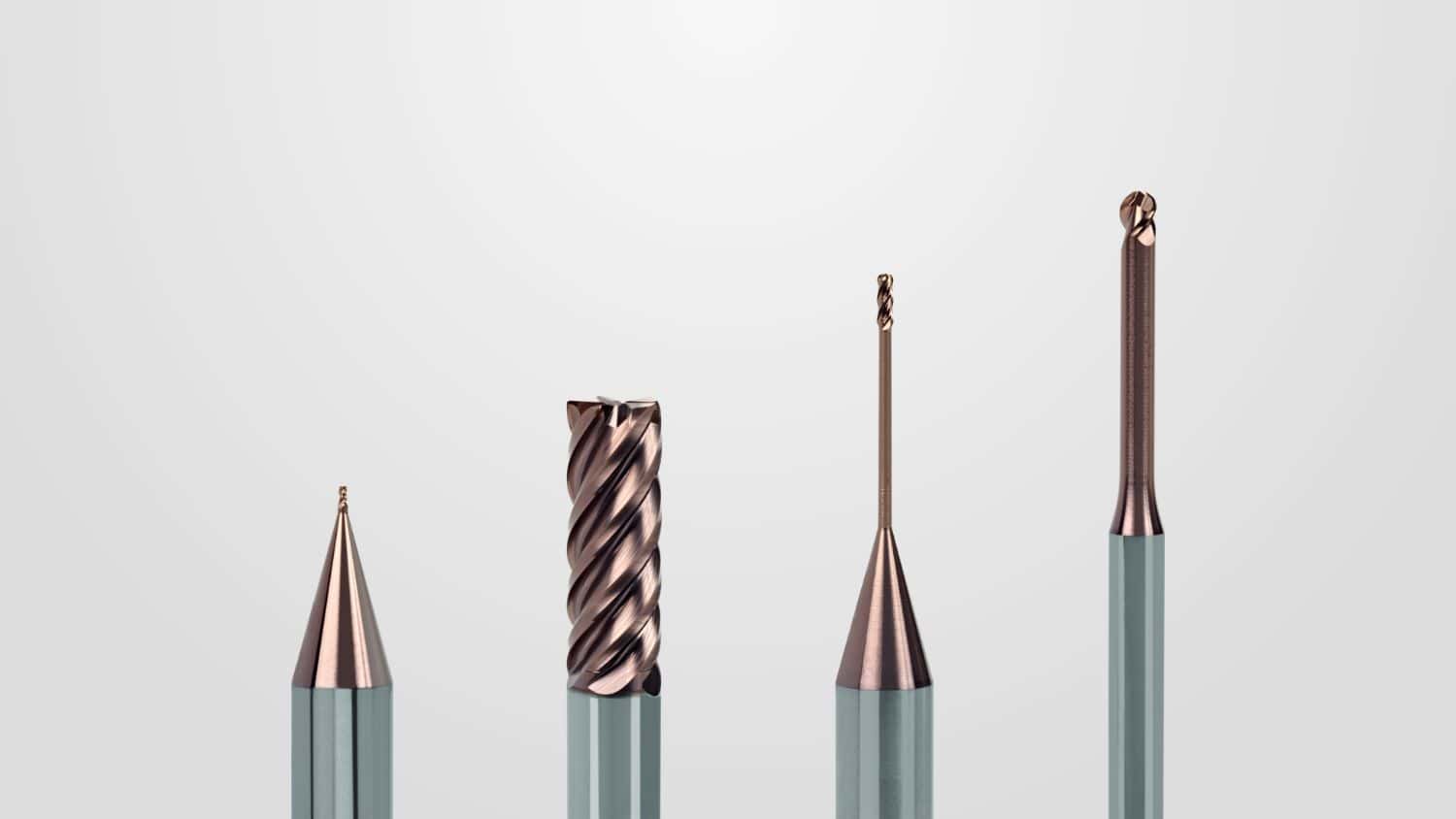
Hard machining, especially the machining of injection molds made of hardened steels with more than 50 HRC, is a demanding application: The materials are both hard and tough, and alloying components that increase corrosion resistance further complicate the machining tasks. “Here, the milling cutters used literally cut their teeth due to enormous feed rates and high temperatures at cutting speeds of up to 250 m/min. At the same time, the highest surface qualities are required even for the smallest contours. In order to machine as economically as possible under these extreme conditions, first-class precision tools are required. A prerequisite for this is, of course, the right coating. With our new HiPIMS coating material SteelCon® we provide the right basis for this,” says Manfred Weigand, Product Manager Round Tools at CemeCon.
Perfect combination for top performance
SteelCon® is the second silicon-doped HiPIMS coating material from CemeCon. While InoxaCon® is excellently suited for machining stainless steel, titanium and difficult-to-machine materials, the coating experts have developed SteelCon® specifically for machining hardened steels beyond 50 HRC. Whether dry or wet, milling, drilling, reaming or threading – SteelCon® is the ideal solution in hard machining thanks to its outstanding properties.
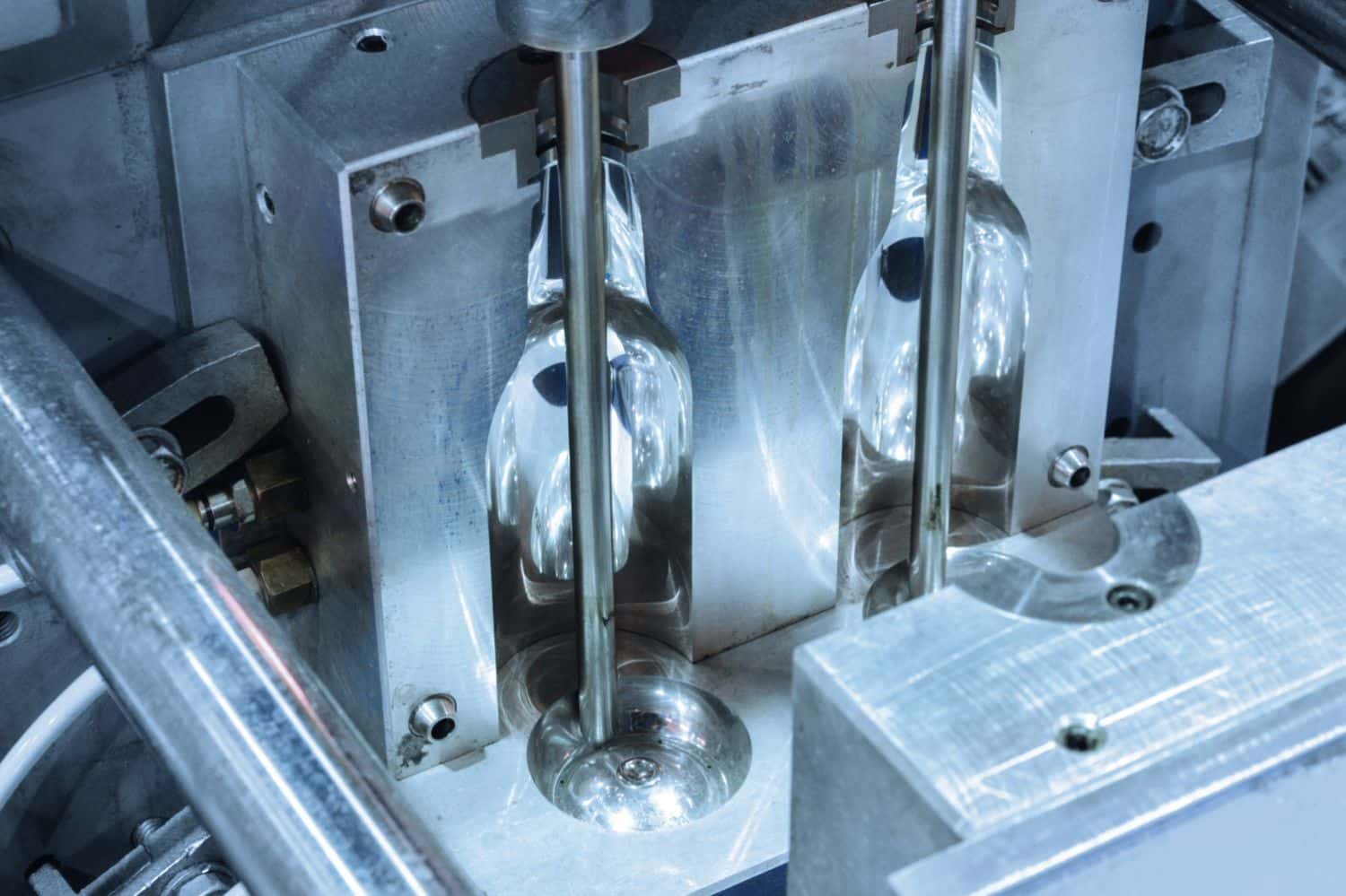
“The HiPIMS coating material SteelCon® is very wear-resistant, on the one hand due to its high hardness, and on the other hand due to its toughness coupled with excellent adhesion. It has a dense layer structure and the thermal stability has been increased. Top conditions for best performance!” emphasizes Manfred Weigand. “Another plus: The wear behavior of SteelCon® differs significantly from other coatings available on the market. Tool manufacturers as well as users are enthusiastic and give us consistently positive feedback: ‘We have never seen such homogeneous wear behavior.’ This ensures high process stability.”
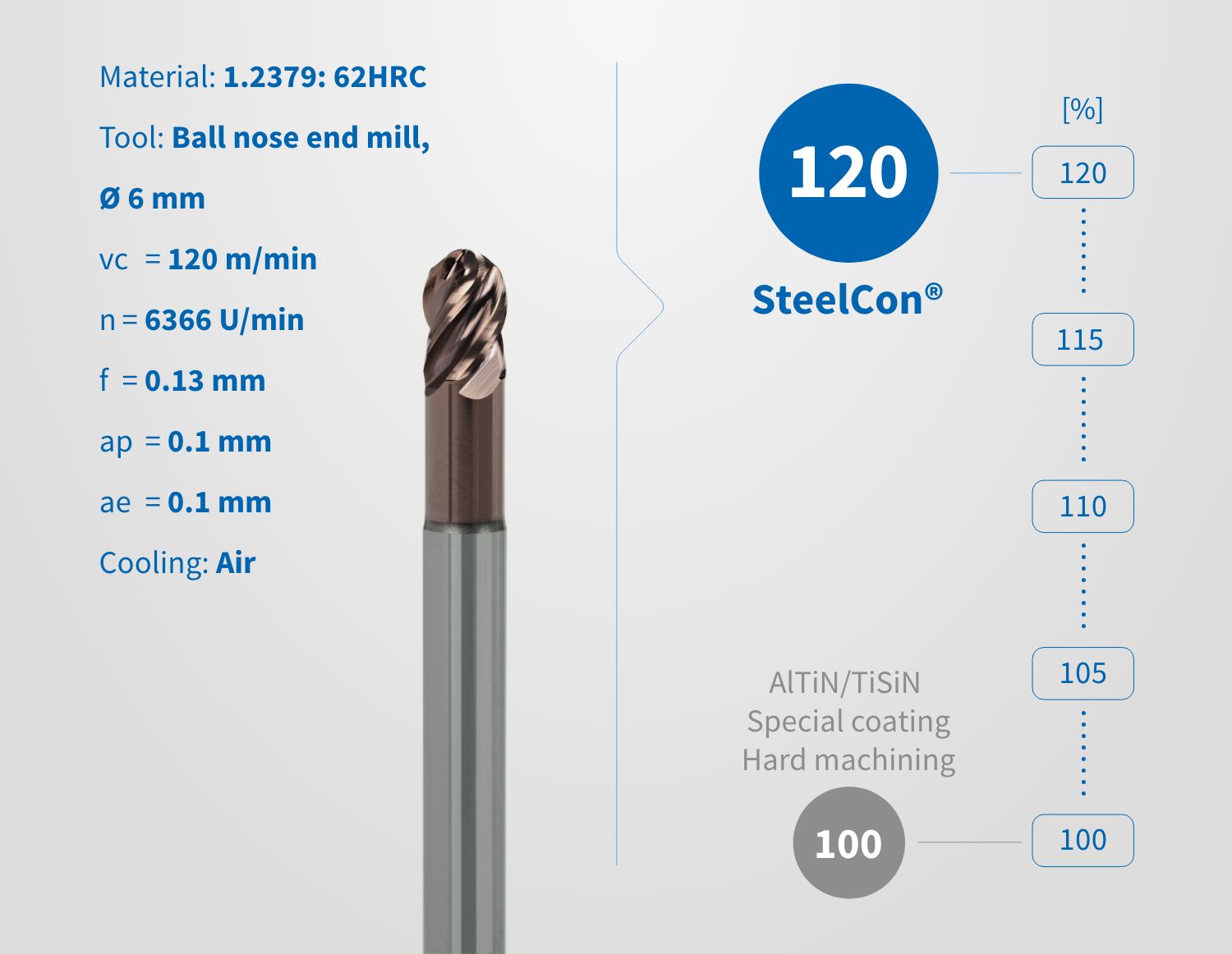
Since no droplets can form thanks to the HiPIMS process, SteelCon® is extremely smooth. This means that nothing stands in the way of optimum chip and heat removal. The tool can dissipate the heat in the chips, and process stability increases. Excellent surface qualities are achieved, so that the user can often save subsequent work – in some cases even the polishing of their workpieces.
Those who use tools with a matched SteelCon® coating when machining hardened steels are on the safe side: Shorter machining times, reduced setup and handling procedures, and better surface quality significantly reduce the bottom line costs. “We achieve such advantages thanks to the extreme hardness, high toughness, smooth surface, maximum adhesion, high thermal stability and dense morphology of SteelCon®,” says Manfred Weigand in summary.
Download this FACTS Story as PDF Overview of all FACTS magazines (PDF)