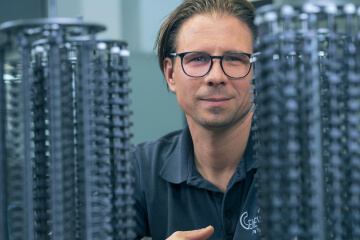
How CemeCon develops competitive advantages for the customer
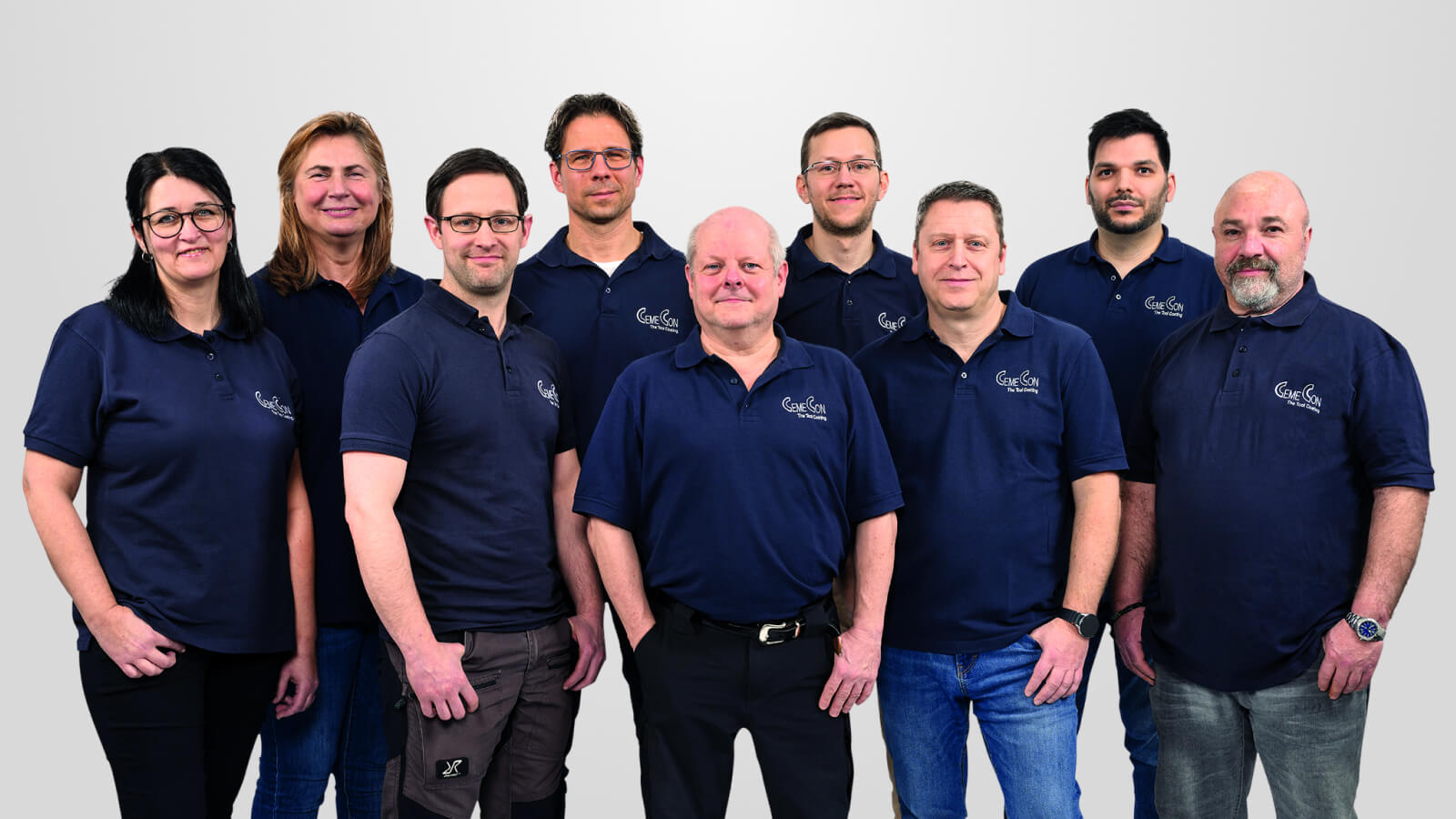
Engineering for customized coating solutions
Modern machining processes require maximum precision, especially in industries such as medical technology, electromobility and electronics. CemeCon therefore relies on customized premium coatings: In engineering, Jürgen Balzereit and his team tailor the coatings to the specific requirements of the respective tools and applications. Stephan Geisen supports this process with his expertise as a materials tester when analyzing the coating. In the interview, both provide insights into their work.
Mr. Balzereit, the requirements in sectors such as medical technology, electromobility and electronics are high. How does CemeCon support tool manufacturers in successfully positioning themselves on the market?
Jürgen Balzereit: Tool manufacturers often come to CemeCon because they want to launch a new tool on the market and are looking for our expertise. Others are pursuing the goal of differentiating themselves even more from the competition. Sometimes that the user’s machining process is not running optimally and the tool needs to be better adapted to the application. Our engineering team analyzes machining results, material properties and tool geometries in order to develop an optimum coating solution. These customized solutions give our customers a clear competitive advantage.
How does such a process work in practice?
Jürgen Balzereit: First of all, we look at the requirements for the tool and the material to be processed. The more information we have, the better we can create a customized coating specification. There are a number of parameters for this: coating material, coating thickness, tolerance, pre-treatment, finishing and much more. The process steps are sensibly combined and individually adapted to the parameters. We work closely together with our customers and rely on sampling: the tools are given different coatings, which are validated in a machining test at the customer’s premises. Only when the best possible result has been achieved do we define a final coating specification that is precisely tailored to the application.
Mr. Geisen, you analyze the coatings in detail. Which role do your investigations play in the engineering process?
Stephan Geisen: A decisive one! Our customers expect consistently high quality, and to achieve this we need to know every detail of the coating. Among other things, we measure the coating thickness, analyze the roughness of the surface and check the mechanical properties such as hardness and adhesion. We use state-of-the-art measurement technology – for example, we use a high-end scanning electron microscope from Zeiss to make the finest details visible. This data helps us to optimally match the premium coatings to the respective machining processes.
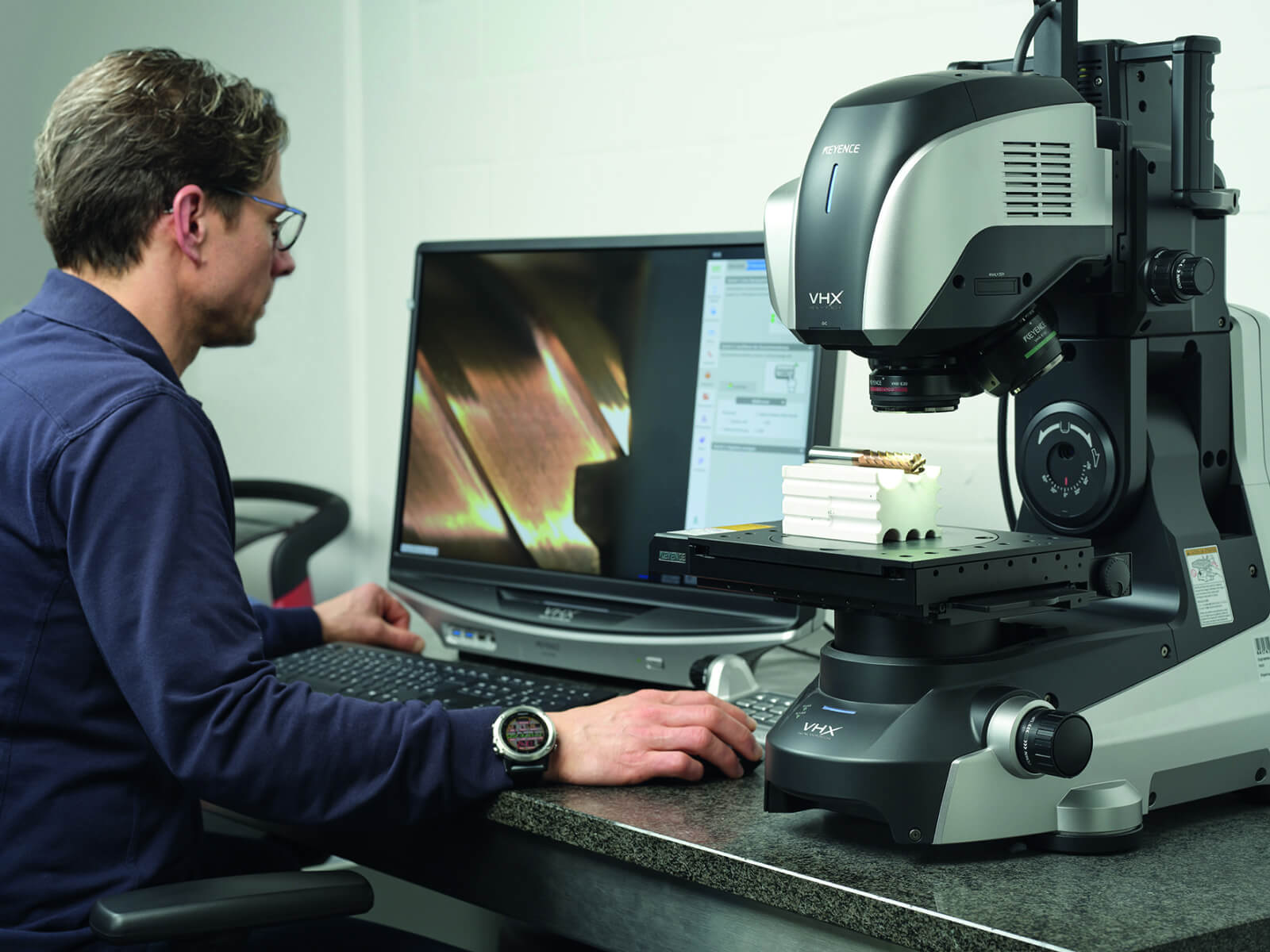
What other test methods do you use?
Stephan Geisen: In addition to microscopic analysis, we use a nano hardness tester from Anton Paar to precisely determine the mechanical characteristics. We check the cutting edges and examine the surface quality of the tools. Incidentally, all successful parameters are stored so that we can reproduce our coatings worldwide with the same quality.
Mr. Balzereit, the interplay between theory and practice seems to play a central role at CemeCon. How do you ensure that each coating MATCHES THE TOOL OPTIMALLY?
Jürgen Balzereit: Our close cooperation with the customers is the key to our success. We involve both tool manufacturers and users in the engineering process. This is the only way we can develop individual solutions that meet the highest requirements. We also rely on a continuous improvement process: our engineering experts optimize the coatings until the best possible result is achieved.
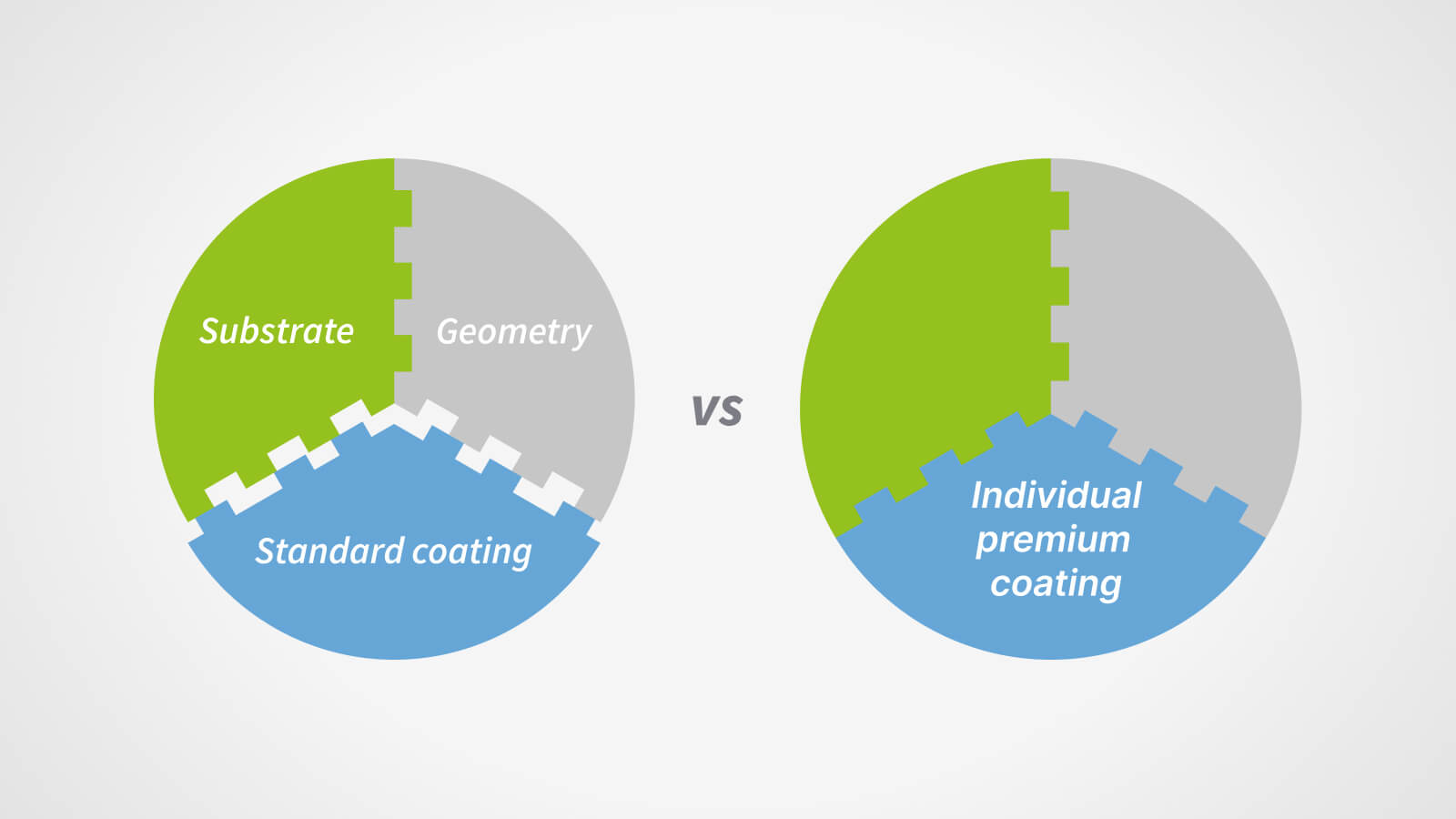