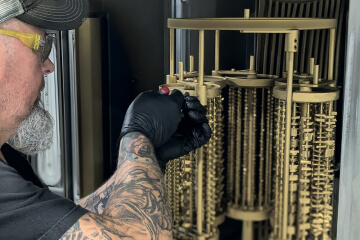
The complete coating process from a single source
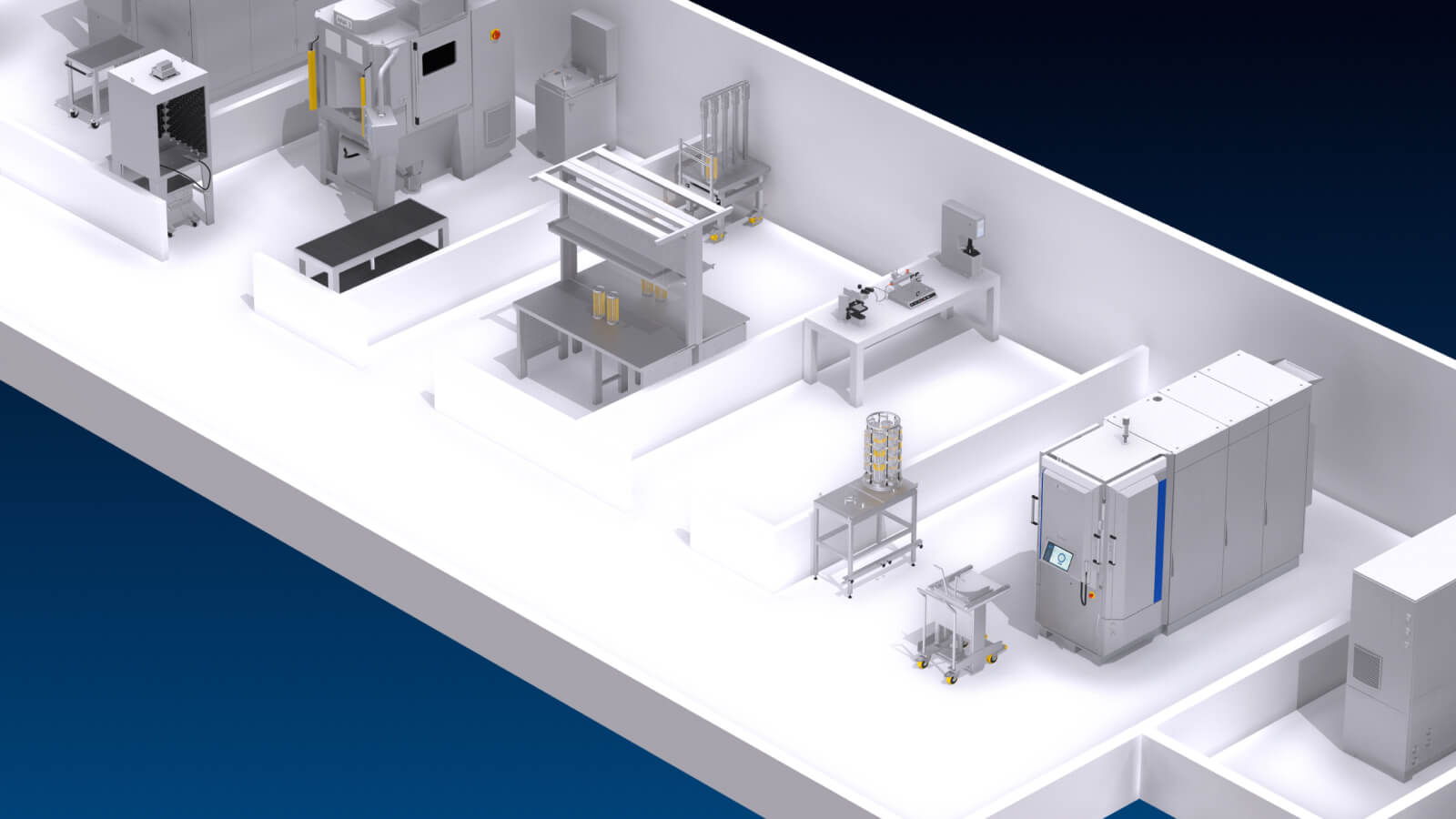
The quality of coatings and thus of coated precision tools depends to a large extent on the optimum interlocking of all necessary process steps. This is why CemeCon offers all components for a complete in-house coating center from a single source – perfectly coordinated. The complete package, consisting of the coating system, substrate pre-treatment and post-treatment, covers the entire workflow. This combination guarantees the best coating results.
With the experience gained from the construction of more than 300 systems, CemeCon takes on the planning of a customized turnkey solution as a project partner. The CemeCon advantage: all components – from the coating system to pre- and post-treatment, quality control and charging – are individually adapted to customer requirements and the existing infrastructure. Even more, they are perfectly coordinated.
The experts can draw on a unique wealth of experience and comprehensive process knowledge to achieve this, as they are coating designers, plant engineers and coaters. In one of the world’s largest coating centers for cutting tools in Würselen, Germany, CemeCon finishes up to 80,000 precision tools with high-quality premium coatings every day. A turnkey solution seamlessly integrates this extensive wealth of experience as well as the proven CemeCon coating materials into the customer’s production.
Everything you need for your ownin-house coating of your precision tools in one place:
Get your personal access to our Web Catalog
Coating
At the heart of a turnkey solution is the CC800® HiPIMS. With coating rates of up to 2 µm/h, coating thicknesses from 1 µm to currently 12 µm and capacities of up to 1,800 shank tools or 5,000 cutting inserts, it is the fastest, most flexible and most economical coating system on the market. It is the perfect platform for developing customer-specific processes.
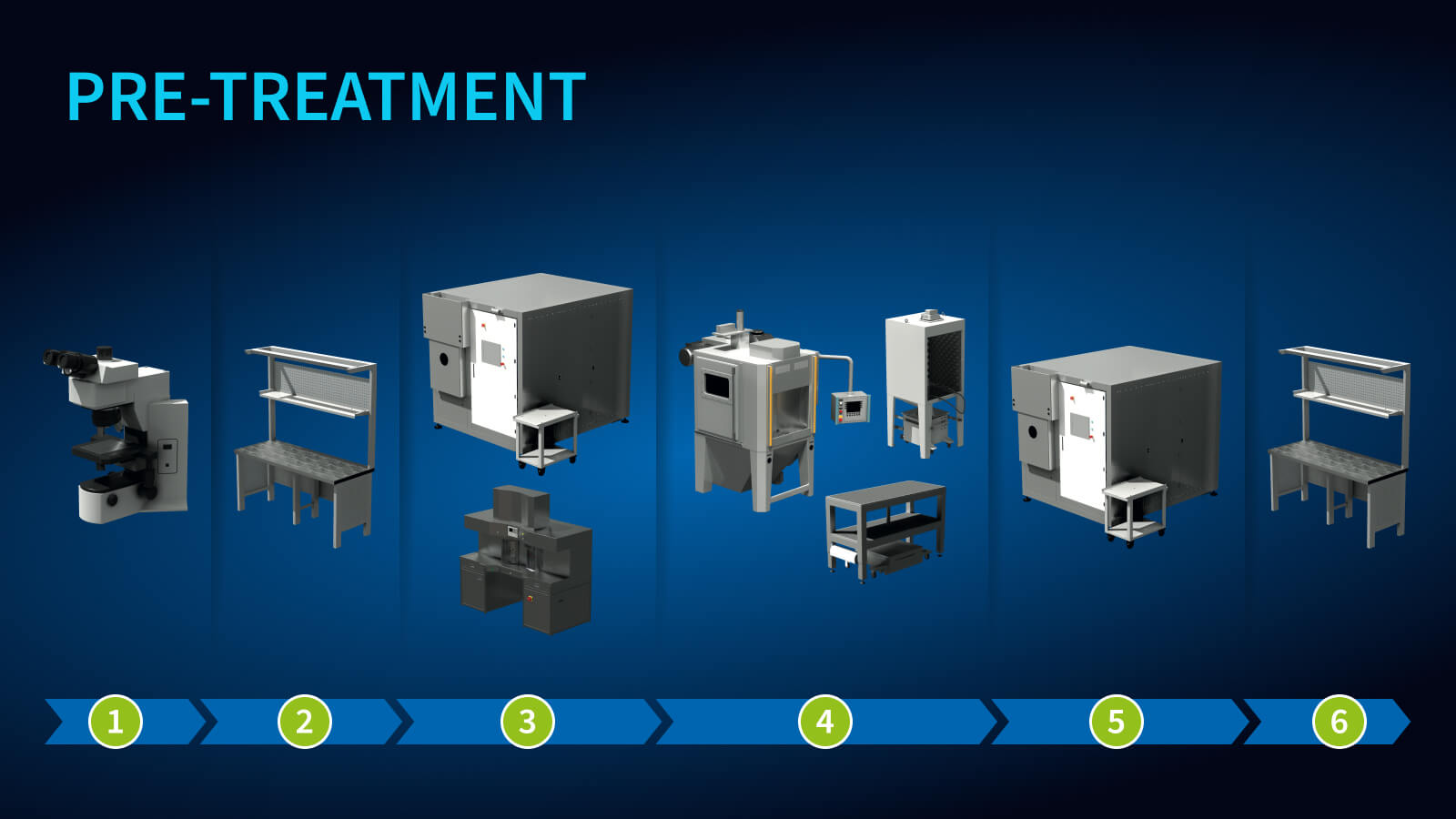
Blasting
Blasting systems optimally prepare the substrate – more precisely the tool surface and cutting edges – for coating. They remove cobalt deposits, burrs and grinding burn from the tools.
Cleaning
The cleaning systems ensure that the tools are cleaned gently. Before coating, they create a clean basis for optimum adhesion. In post-treatment, residues from any finish can be completely removed.
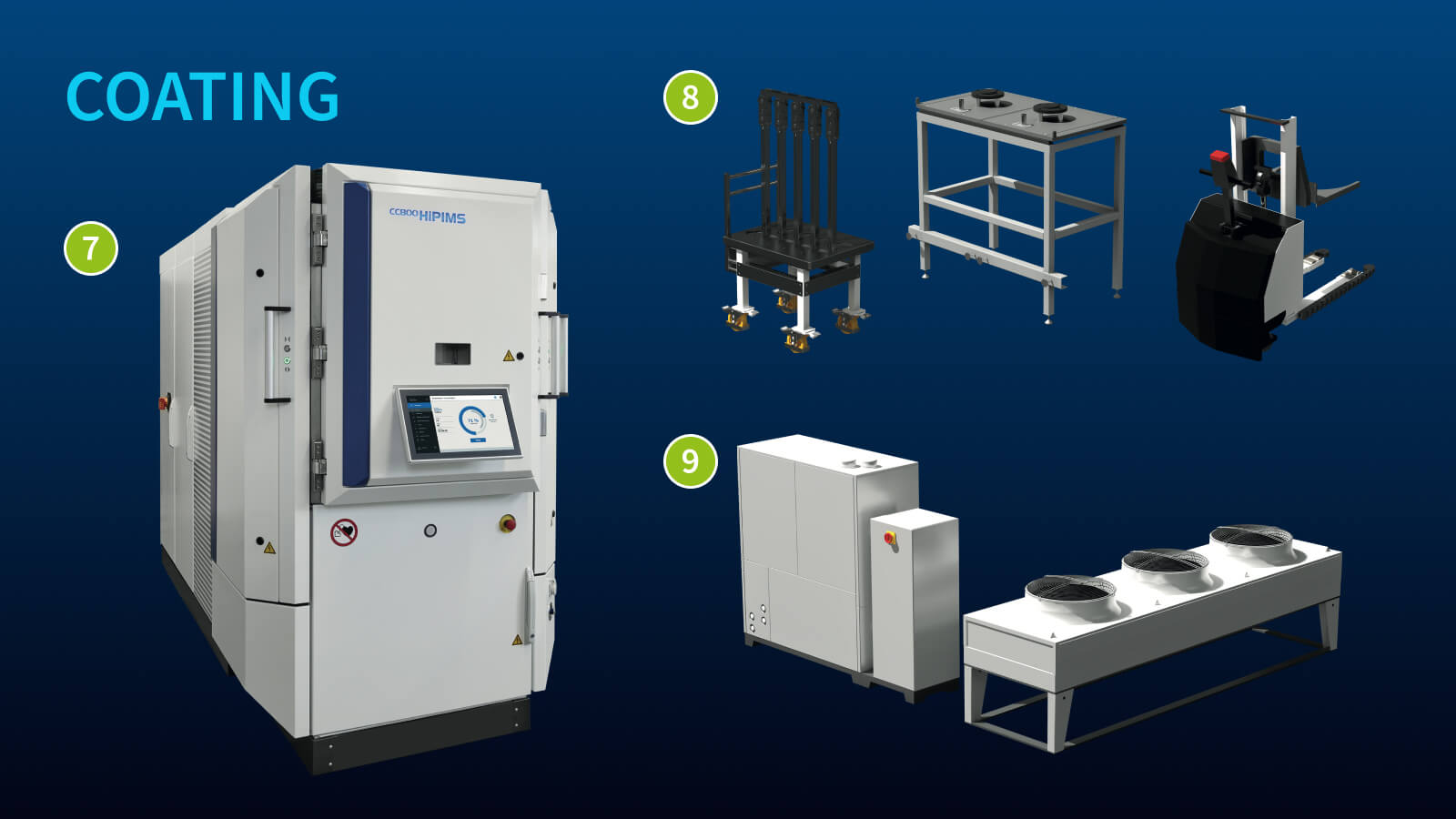
Quality control
Good output quality is the basis for good perform ance: this is why CemeCon offers numerous suitable test devices for customized quality assurance.
Cooling
Cooling systems dissipate the heat generated during coating and thus ensure the necessary process reliability. CemeCon offers reliable, compact and energy-saving cooling systems for every system size and coating technology.
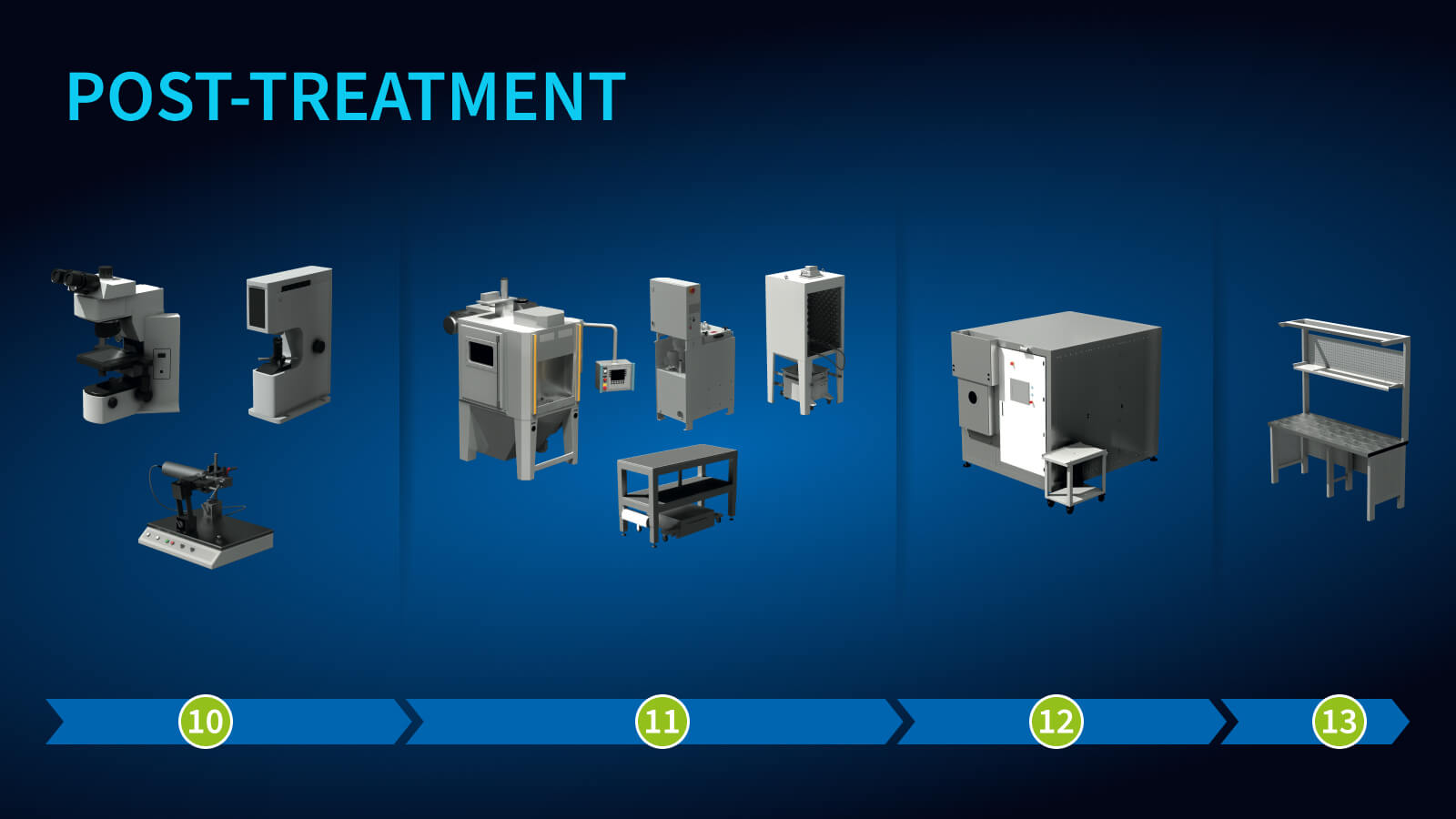
Batching
With years of practical experience from its own coating service, CemeCon has developed perfectly matched holder systems for different types of tools, which ensure optimum utilization of the systems in pre-treatment, coating and post-treatment.
Finish
With coordinated finishing processes, the tool surface and cutting edges can be optimally post-processed.
Download this FACTS Story as PDF Overview of all FACTS magazines (PDF)