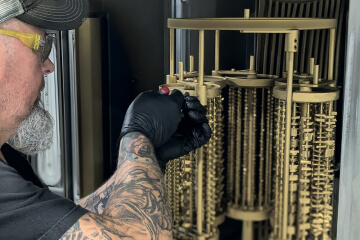
High-performance CemeCon coatings – even in extra-thick
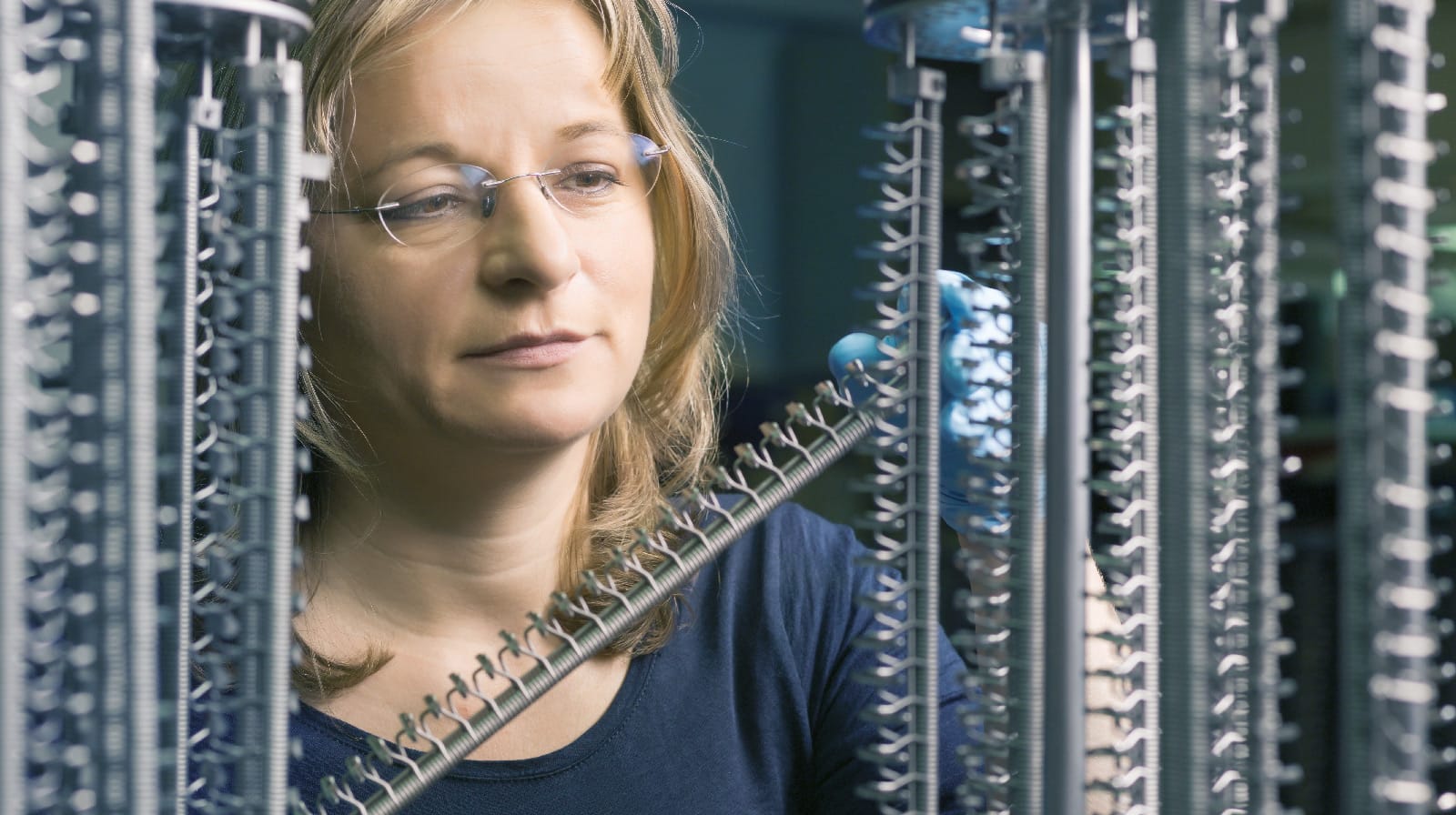
HiPIMS premium coatings for cutting inserts
Milling and turning cutting inserts, any way you like. They machine all imaginable components: whether gears for wind turbines weighing several tons or turbine blades for aircraft engines. The smooth, hard and at the same time tough HiPIMS coatings from CemeCon are the key for maximum performance when processing the hardest, most challenging materials. Extra thick coatings make much longer service lives for tools possible.
FerroCon®, InoxaCon®, AluCon® – this family of coating materials is the current top favorite for premium coatings of cutting inserts. And for good reason. “With HiPIMS technology, tool manufacturers don't need to compromise anymore. HiPIMS combines the advantages of all PVD coating processes: denser coating morphology, harder coatings, lower residual stress in the film, excellent adhesion, and thermal stability”, explains Inka Harrand, product manager for cutting inserts for CemeCon. The positive machining results of many customers supporting that statement.
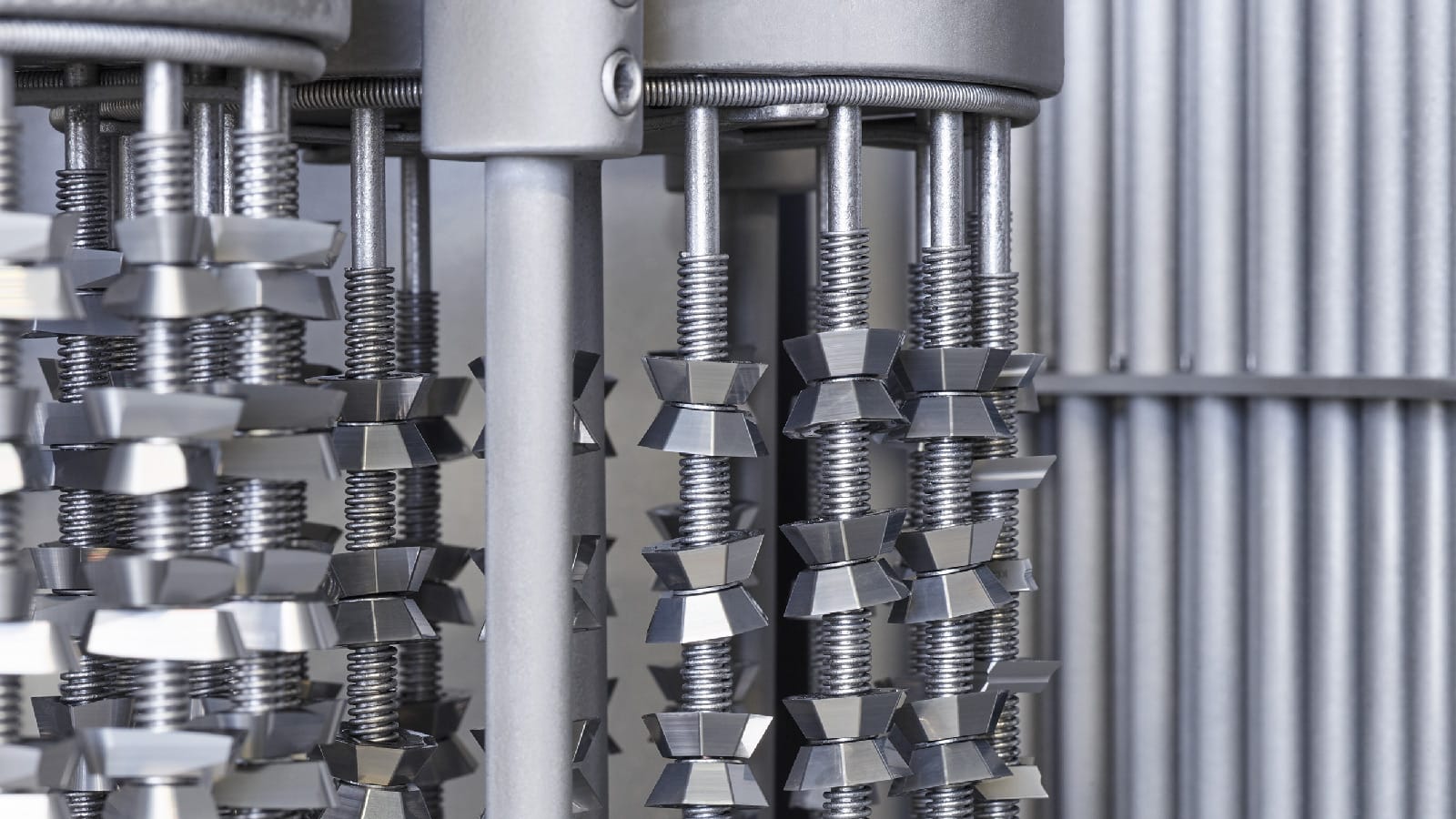
HiPIMS is the rigorous further development of the sputter process proven at CemeCon for decades. Harrand is convinced that “for developers, the technology offers enormous potential. In principle, almost any material can be deposited with HiPIMS: the direct transfer from solid state into plasma overcomes the limits of traditional methods.” An enormous flexibility that helps anyone working on new products and solutions.
Also in extra thick version – with HiPIMS, even better
Excessive residual stress restricts coating thickness to a mere 3 µm for conventional coating processes. HiPIMS is game-changing. The plus variants of FerroCon® are more than twice as thick at 8 µm. “And thanks to the grain refining effect of HiPIMS technology, the thick coatings are denser, more regular, and tougher than before. This has even more positive effects on service life,” explains Harrand. Additional plus: The high metal ionization produces a very uniform coating distribution all over the insert with excellent coating adherence on complex tool geometries.
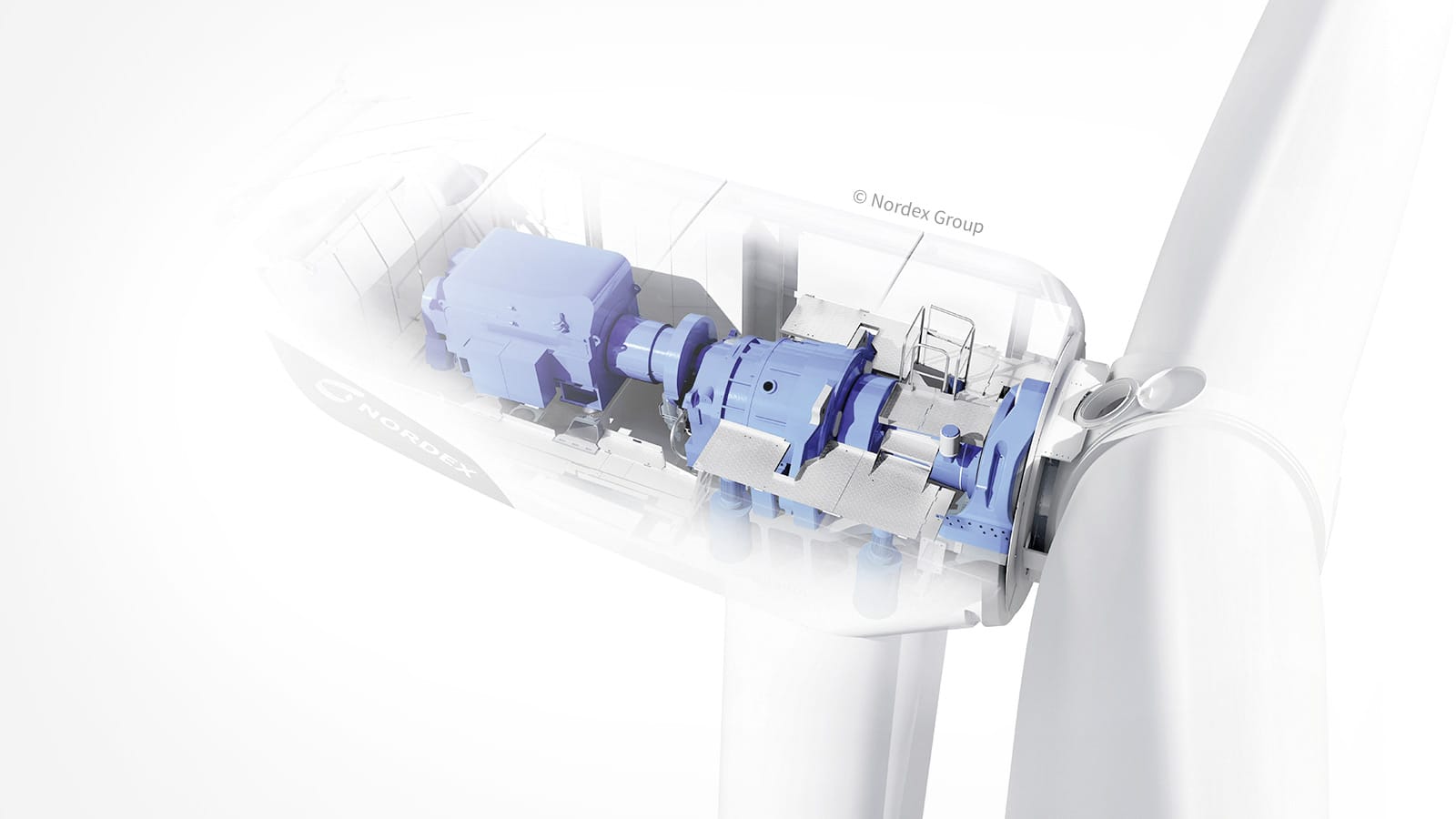
Own production line for greater process stability
For the coating process of cutting inserts, CemeCon has set-up its own production line in the coating center. Batches of cutting inserts and shaft tools are processed completely separately. “That is possible because we have the world's largest coating center here in Würselen,” says Harrand, looking around the plant. “We are convinced that this individual treatment benefits the quality of all tools. Our users very much appreciate that we have the capacity to coat small inserts,” she says holding her fingers a few millimeters apart; “and much bigger shank tools in separate batches with appropriate coating processes.”
Download this FACTS Story as PDF Overview of all FACTS magazines (PDF)